Manufacturing leaders have lately realized the importance of technological advancements such as Artificial Intelligence and Machine Learning. While the leaders have started implementing industry 4.0 across their manufacturing networks, a majority of industrial OEMs still struggle to capture the full potential of their transformation efforts, attain maximum ROI and maintain a competitive edge.
With an innumerable amount of investment, time, and effort going into digital transformation, some businesses are enjoying benefits such as increased production capacity, improved delivery lead times, reduced environmental impact, and improved customer service. But the journey to digital transformation is still not a cakewalk.
In this article, we’ll explore:
- What digital transformation means for manufacturing.
- Why it’s difficult yet necessary
- Challenges faced by manufacturers
- Practical solutions for overcoming transformation hurdles
What Is Digital Transformation in Manufacturing?
We live in an era of unprecedented technological innovation; the time when you can’t succeed if you are not well versed with technology trends. And yet according to Forrester Research, only 12% of the Fortune 500 companies from 1955 remain Fortune 500 companies today. You know why? Because only 27% of businesses have a coherent digital transformation strategy that brings out the customer value in place.
Digital transformation in manufacturing is the integration of advanced technologies into core business processes to drive innovation, efficiency, and value. It’s about transforming operations, products, and customer interactions using data-driven insights, automation, and connectivity.
Key Components Behind the Driven Value
AI and Machine Learning: Drive predictive maintenance and operational insights
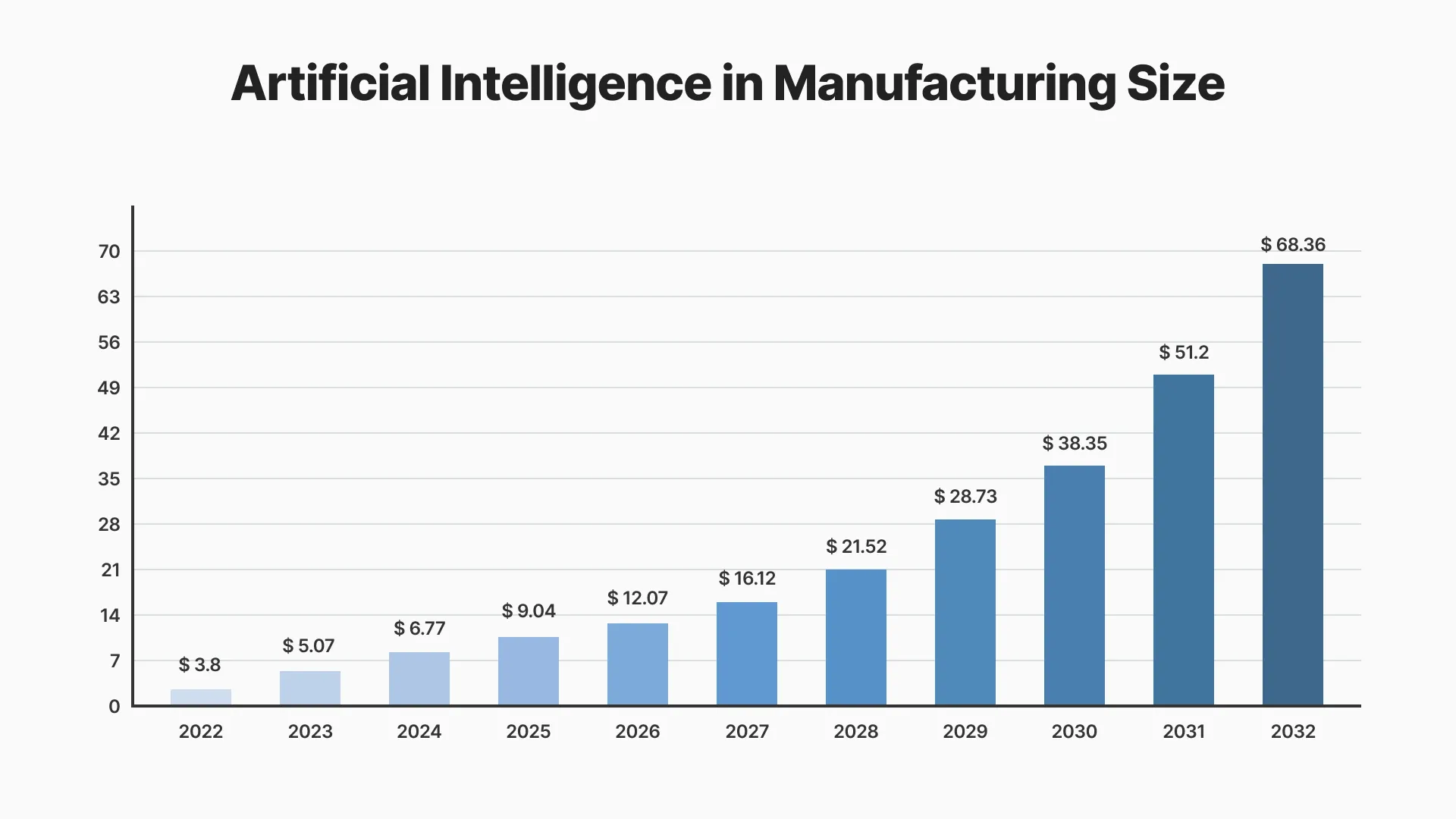
Industrial OEMs are becoming more efficient. The reason behind it is AI ML-powered digital transformation which is making them smarter and streamlined. AI, ML models automate tedious processes, making them more efficient without manual interventions. Using these technologies manufacturers can predict trends and improve the quality of their products as well as have complete control over their supply chain. Using tech trends like AI and ML, OEMs can analyze customer data to find patterns to predict equipment failure, define maintenance roadmap, and forecast the customer demands.
Cloud Computing: Provides scalable storage and computing power
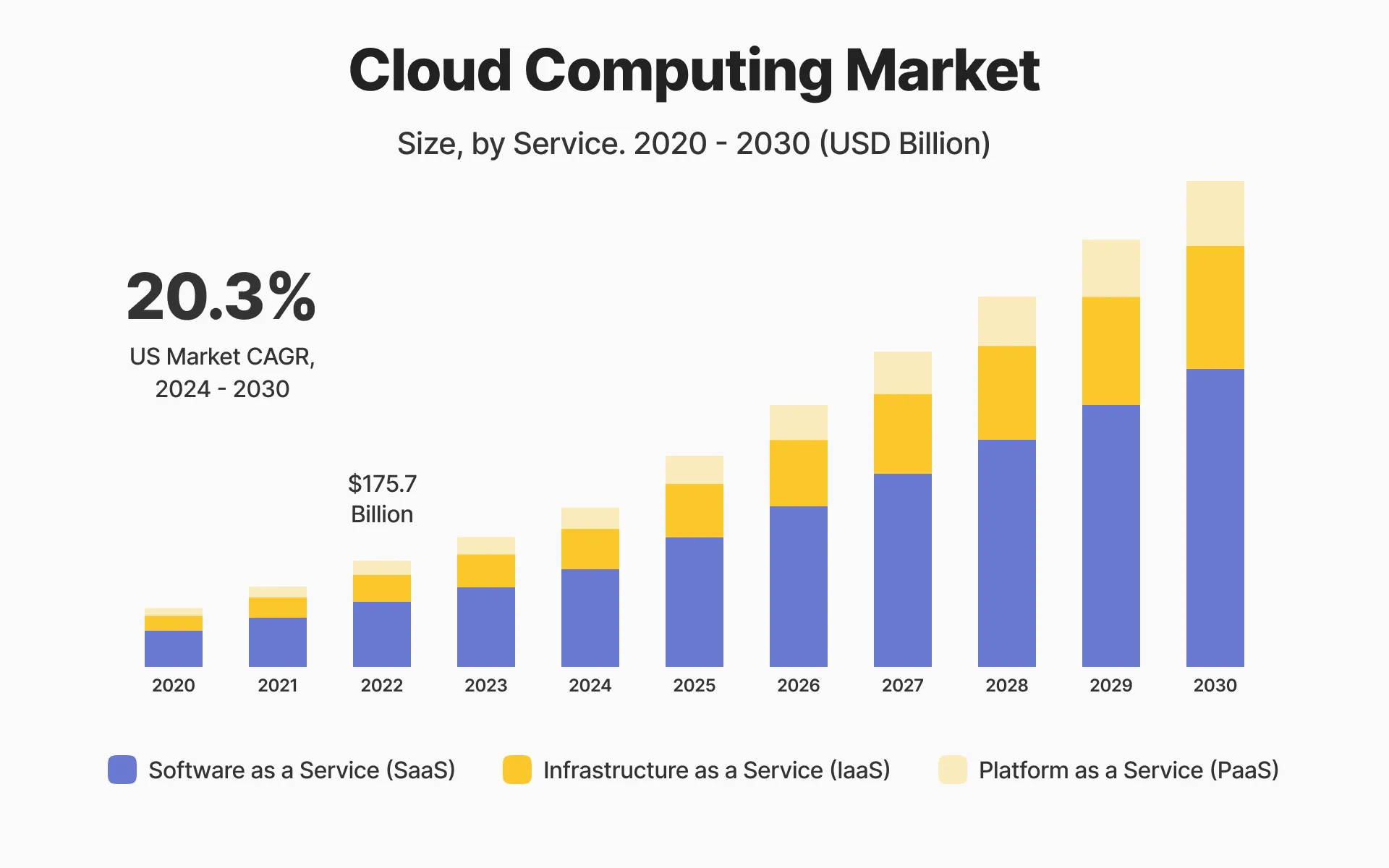
Cloud computing has emerged as a centralized force driving a ‘digital-first’ environment, offering businesses the necessary scalability and flexibility they need for rapid innovation. With cloud computing, it is easier to launch new applications and services. Since cloud-based applications facilitate collaboration irrespective of geographical locations, it can enhance productivity and efficiency.
Big Data Analytics: Facilitates informed decision-making through real-time insights
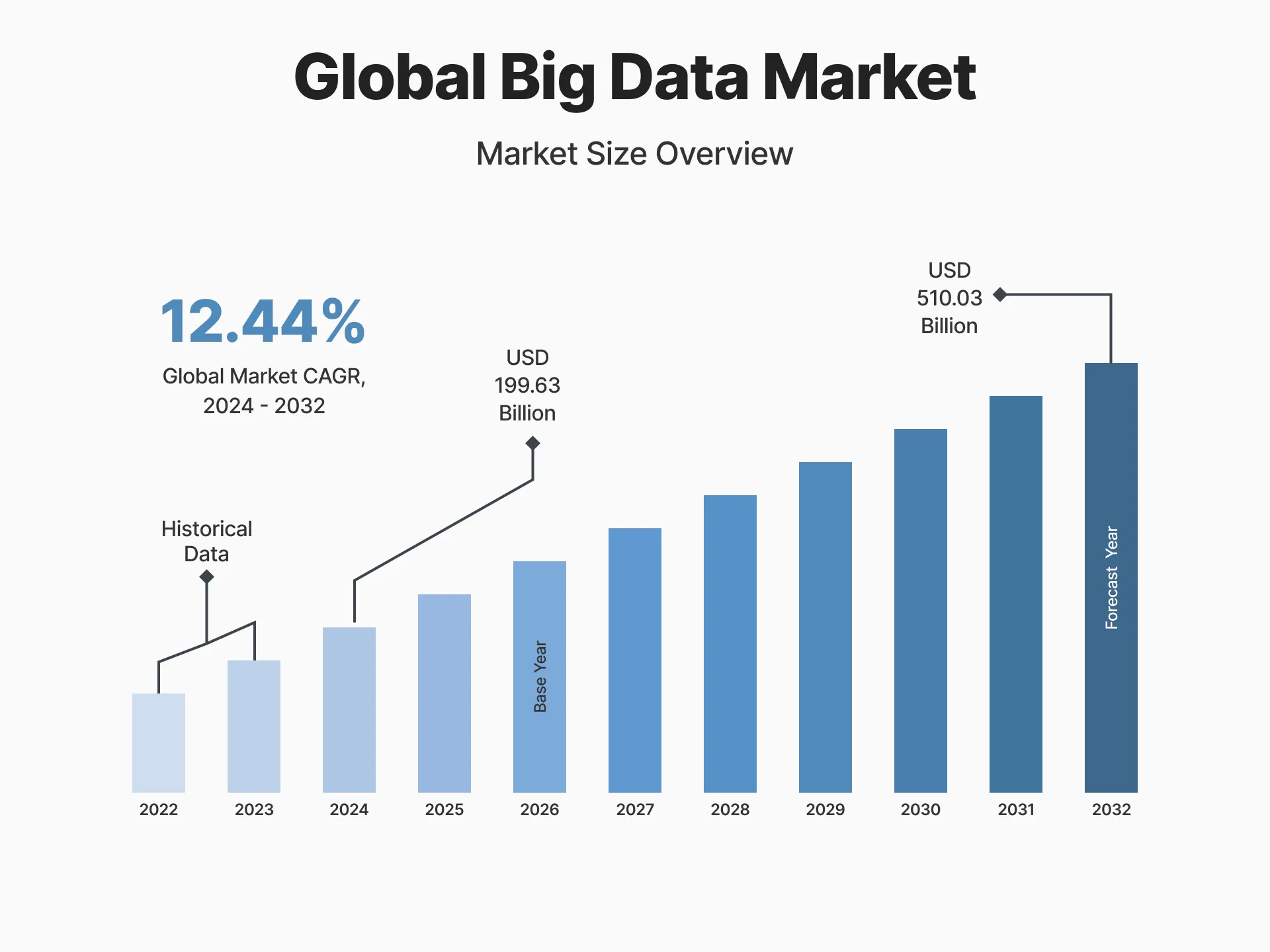
Big data means the vast volume, variety as well as the velocity of data businesses generate and collect. Data has become an important part of OEM’s operations as it helps in measuring performance and improved efficiency. Using big data, manufacturers can identify market trends, have real-time insight into their business processes, and make informed decisions. This further helps in improving product development, supply chain management, and overall manufacturing processes.
Why Is Digital Transformation in Manufacturing Difficult?
Despite its advantages, implementing digital transformation in manufacturing is a complex endeavor.
Key Challenges while implementing digital transformation processes
- Change management isn’t easy: From what successful businesses have talked about carrying the digital transformation initiative, change is the only constant recipe to success. Digital transformation is a long-term process; it does not happen overnight no matter in which archetype of the spectrum you are. Businesses need to develop a governance plan, implement cross-functional groups and representatives who can provide visibility on the transformation initiatives and progress.
- High Skill Shortage for Digital Innovations: One of the major challenges manufacturers while developing their strategy for digital transformation is ensuring their employees are the pace to adapt to technological transition. What a successful manufacturing business needs is building a digital team capable enough to develop custom, scalable IoT solutions. The core expertise of manufacturing businesses has never been into software development and building a digital team capable enough to develop a major platform in-house becomes a real challenge. Complex technologies require resources with specialized skillset. The successful OEMs maintained a small digital team of experts to ensure synergy with a software technology partner.
- Significantly Higher Implementation Costs: Digital transformation can be costly for many businesses because it requires spending on specialized software, skilled personnel, onboarding and integrating new technology into existing systems, and multiple such factors. As per Deloitte, 62% of organizations view cost as a barrier to digital transformation. But at the same time, they also need to understand the long-term benefits and return on investment. According to McKinsey, businesses that spend on riding the digital transformation wave are 23% more profitable than the ones that are still skeptical about it.
- Data Silos: Digital transformation is a centralized approach and at the center of all is data. 3 out of 4 executives have said an effective data strategy across the enterprise can help them achieve their digital transformation goal. But there is still a long way to go for many multiple businesses. They need to understand the systems where the data lives, need to gain accessibility of the data, improve connectedness, break data silos, and gain real-time data insights to successfully implement digital transformation strategies. Manufacturers need to adopt a proper data management strategy and implement AI-ML to gain accurate data insights in order to maximize the full potential of their business processes.
- Choosing the Right Technology Partner: Digital transformation for businesses is not just about moving from the current technology to another, it is a continuous process that involves multiple steps. All this can’t be done by an organization alone. You need a trusted technology partner who can provide you with the necessary support to achieve your long-term business goals. You must have a partner who has expertise in your domain and ensures your business is on par with the latest technological disruptions.
How Digital Transformation Impacts the Manufacturing Industry
Digital transformation has profound implications for the manufacturing sector.
- Predictive Maintenance (PdM): They say it right: Prevention is better than cure. The onset of digital technologies has enabled the approach from waiting for failures to happen to fix it before it happens. A Predictive Maintenace (PdM) solution could be the savior for any industrial manufacturer with high-capital assets looking to control rising equipment maintenance costs. The new gen manufacturers are already using advanced technologies to not just continuously monitor data but employing advanced algorithms to take actions based on that data. PdM offers you the opportunity to boost operational efficiency. With automating processes through ML and cognitive data science, you can reduce maintenance costs and equipment down-time, improve worker safety, and revolutionize the entire inventory management system.
- Supply Chain Optimization: For smoother production, processes, and operations, manufacturers need a connected supply chain. Any possible disruption could impact the inventory, trust among the suppliers and partners, time to market, and ultimately affect the business reputation. With digital transformation, OEMs can have better visibility into their supply chain and plan for future challenges. With smart automation and data-driven insights, it is easier to collaborate and respond to market changes and boost operational efficiencies.
- Reduced cost: Reducing cost is a necessary goal for manufacturers. The cost of production, materials, and transportation has an imperative effect in decreasing the overall product profit margin. Digital transformation has proved to pave new pathways to develop parallel revenue streams through additional business models such as Equipment as a Service and SaaS enablement. These technological adoptions also allow organizational stakeholders to make cost-effective decisions and ensure business sustainability.
- Reduced time to market: Industrial OEMs can leverage digital transformation to significantly reduce time to market by adopting advanced tools and technologies. Industrial solutions built on custom IoT platforms integrated with advanced analytics, machine learning, and failure analysis, play a pivotal role in streamlining operations at OEM’s customer sites. These technologies enable OEM customers to simulate processes and equipment lifecycles, identify potential issues early, and optimise workflows, ensuring faster and more efficient outcomes.
- Improved CX: With evolving digital technologies, manufacturers can improve product quality, deliver high-level services, and enrich customer experiences. By leveraging digital transformation initiatives, they can predict what their customers are looking for and create products and services based on market trends and customer demands. For example: With data analytics, they can analyze customer data and gain insights into their needs and preferences. Using this, they can create equipment with customer-aligned features, ensuring customer satisfaction excellence. With added services to their offerings, they can build long-term customer relationships. Digital platforms also help manufacturers facilitate direct interactions with their customers, which improves the scope of feedback.
- Improved decision making: Digital transformation is changing the course of decision making for manufacturers. Instead of a reactive approach, businesses are shifting towards the proactive approach. Data-driven insights such as analyzing and interpreting the trends and patterns, provide them with the accessibility to take decisions not just based on predictions but logic. With Asset Lifecycle Management (ALM) solutions, manufacturers do not have to wait for asset failures to take action, instead they can manage the entire lifecycle from asset inception to asset reclamation. This not only minimizes asset downtime but also helps OEMs save millions of dollars.
- Competitive edge: Digital transformation helps businesses manage asset lifecycle, enhance efficiency, reliability, and bring sustainable business operations. Manufacturers who are ahead in technological adoption are creating a space for themselves while the laggards are still trying to keep pace with technology. Without going digital, they might fail in terms of cost-effectiveness and delivering customized solutions. Embracing technological disruptions allows industrial OEMs to know what their customers are demanding, optimizing operations, establish smart inventory systems, and improve supply chain efficiency. This all sums up to one thing: being the best out of the lot. When you are delivering what your customers expect from you, you are building relationships that last longer than your competitors.
- Sustainability: With industrial IoT allowing real-time asset remote monitoring, tracking energy consumption, asset performance, it ensures businesses understand the environmental impact of their equipment better. With energy management systems, OEMs can deploy smarter equipment that is not just business friendly but also meets the environment and customer data protection compliances globally.
Simplifying Your Digital Transformation Initiatives
For OEMs seeking a simplified yet powerful approach to enable digital transformation, custom IIoT platforms stand as the bedrock to build and deploy enterprise-ready solutions.
The Flex Platform allows you to build a secure and scalable multi-asset handling application suite – simplifies the complexity of big data deployments, turning them into cost-effective, streamlined pathways to faster ROI and use-case realization. From asset management and IT/OT optimization to service automation and introducing smarter product lines backed with big-data analytics to seamless system integration, as OEMs adopt next-generation operational technology centers, Flex83 provides a smooth, future-proof transition, enabling you to confidently navigate the evolving landscape of digital transformation.
Conclusion
Digital transformation is no longer an option for industrial manufacturers—it’s essential for survival in today’s rapidly evolving market. By embracing technologies like IoT, AI ML, and Data Analytics, industrial OEMs can unlock unprecedented business models, enhance customer satisfaction, and achieve sustainable growth.