In the fast-paced world of manufacturing and steering technological disruptions, industrial OEMs need to maximize efficiency and minimize downtime to gain a competitive edge. Your machines with critical jobs and components might experience frequent downtime due to unexpected breakdowns. In some industrial scenarios, even one critical failure could negatively impact your customer’s operation schedules, increase repair or warranty costs, and affect the overall delivery timeline, causing significant losses in both revenue and customer satisfaction.
With a defined ALM strategy in place, the equipment manufacturers can take a proactive and long-term approach. They can use the IIoT-enabled predictive analytics to monitor the asset health, track machine metrics such as temperature, vibration and use this real-time data to predict and prevent possible downtime.
This article will help you understand the concept of Asset Lifecycle Management and why your industrial OEM business needs smart solutions against the ever-evolving technological disruptions.
Why IoT Asset Lifecycle Management is crucial for OEMs
The current technological disruptions are forcing OEMs to stay ahead of their competitors, and this can only happen when they have complete control of their asset's lifecycle. Again, without ALM, it is impossible. There are multiple challenges OEMs face when it comes to managing their connected assets, but they can’t deny it is crucial for them.
- Security: The vast amount of connected assets also invites opportunities for cyber threats. Having a robust ALM strategy ensures security measures at all stages, safeguarding multiple assets from potential threats and protecting asset data.
- Scalability: As OEMs plan to scale, they need an ALM strategy that aligns with their expanding IIoT ecosystem and growing assets. Having a well-defined approach can help in seamless integration of new assets as well as facilitate the growth of existing ones.
- Data monetization: The data from connected assets is extensive and valuable. An effective ALM strategy simplifies IIoT data integration that helps OEMs leverage the data to develop innovative services, optimize product offerings as well as generate new revenue streams.
Phases Of IIoT Asset Lifecycle Management
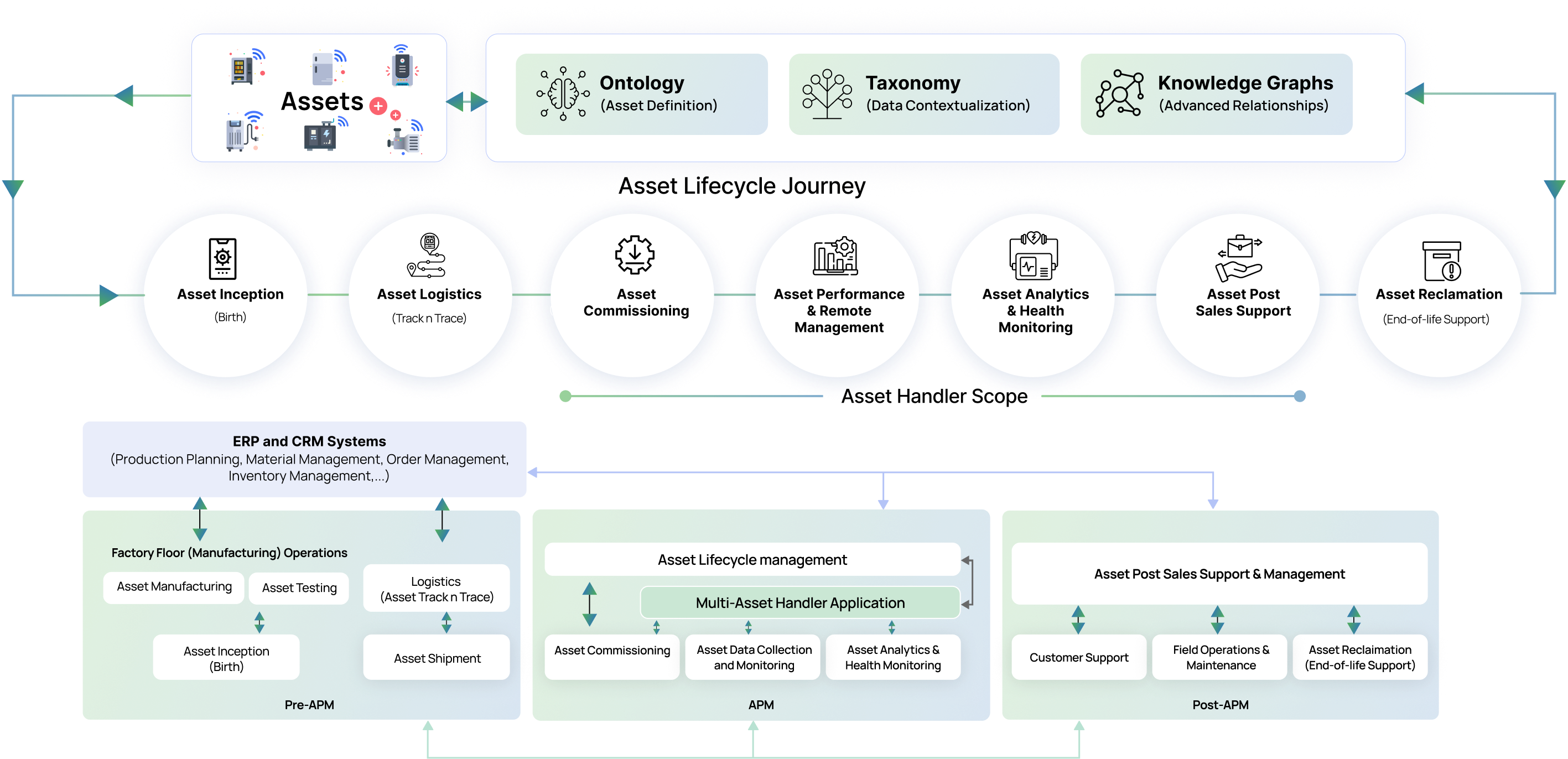
For industrial OEMs, the evolving digital space presents opportunities to transform the asset management entirely across every phase of the lifecycle. However, they can’t just rely on data collection to manage their assets; but the real requirement demands structured data handling as well as actionable insights. To create a robust framework, they would need to track, monitor and manage the assets from inception to reclamation.
Let’s explore each stage in detail:
1. Asset Inception (Birth): This initial stage of the asset lifecycle management journey involves manufacturing and defining the asset’s essential attributes. It includes quality testing, compliance verification, and the creation of a digital identity for every asset. This is where a robust ontology is crucial for defining assets accurately, setting the groundwork for subsequent data handling. In this stage, assets are integrated with existing ERP and CRM systems for material and inventory management.
2. Asset logistics: Once the asset is identified, the next step involves tracing and tracking the assets. Effective logistics management ensures the asset reaches its intended location in the right condition. OEMs need to track data asset data must be captured and stored for transparency and traceability, aiding in efficient resource management.
3. Asset commissioning: At this stage, the asset is prepared for operational readiness. It undergoes multi-asset handling checks, including connectivity set-up to ensure optimal performance when it reaches the customers.
4. Asset performance and remote management: This stage involves monitoring and optimizing asset performance in real-time. Optimizing asset performance also includes fine-tuning of the operational parameters and processes that can enhance the efficiency and productivity of the assets. Leveraging performance monitoring and predictive analytics helps in preventing downtime and increasing asset lifespan.
5. Asset analytics and health monitoring: In this phase, the data analytics tools capture, collect and analyze real-time data on asset health. Asset health monitoring also involves tracking and analyzing asset failures by configuring the failure patterns, root causes, and recurring issues. Using these data patterns, businesses can take strategic decisions, identify and implement preventive maintenance strategies to mitigate future asset failures.
6. Asset post-sales support: The asset enters the post-support phase, where OEMs can provide value-added services to their customers. This stage involves efficient field operations, customer support, and periodic performance checks.
7. Asset reclamation: At this phase, the assets that are no longer economically viable undergo reclamation. This includes dismantling, recycling and environmentally responsible disposal or reusing the valuable components of the assets.
Benefits of Asset Lifecycle Management
Every deployed asset matters when it comes to running a business smoothly, especially when we speak of a huge customer base or hundreds of thousands of assets. Businesses are under constant pressure to do more with less, to enhance customer service, to improve asset uptime, and to increase asset performance. It is not only about ensuring operational excellence but increasing the Return on Investment (ROI). This is all possible only when they know they can keep track of every step of the asset journey but also maximize the full potential of their assets. Having a defined ALM helps in:
- Increased asset utilization
An effective ALM strategy helps in analyzing if the deployed assets are utilized up to their full potential. By continuously monitoring these assets and utilizing the information collected via IoT devices, businesses can measure the performance in real-time and also identify more opportunities for innovations. With the approach of preventive maintenance, they can repair the assets before breaking down or replace them when breaking
- Reduced cost
Asset Lifecycle Management plays a crucial role in reducing the hefty costs involved in asset repair/replacement. With regular remote monitoring, assets can undergo scheduled maintenance based on real-time insights instead of waiting for the equipment to fail.
- Extended asset lifespan
Asset lifecycle management allows you to monitor each stage of an asset’s operation, providing insights into optimal maintenance timing and methods. With a proactive maintenance schedule in place, you can maximize the asset's performance and ensure it stays in peak condition.
- Enhanced Customer Satisfaction:
By leveraging real-time data and predictive analytics, a connected asset lifecycle management approach enables proactive maintenance and swift issue resolution. This results in improved service reliability and strengthens customer trust, as organizations can address potential issues before they affect performance.
- Legal, Regulatory, and Statutory Compliance:
Connected asset lifecycle management systems provide comprehensive tracking, documentation, and monitoring capabilities that support adherence to industry regulations and standards. This minimizes the risk of non-compliance penalties, helping organizations maintain a strong standing with regulatory bodies.
- Improved Safety:
Continuous monitoring of asset conditions allows for early detection of potential risks and hazards. With connected data, organizations can quickly address these issues, creating a safer workplace that safeguards both personnel and equipment through preventive action.
Enhance ALM Efficiency with Data Analysis
While some time ago, managers and operators used to rely on excel and spreadsheets to fulfill their goal of managing assets, recording asset data and carrying out these practices, it changed with ALM solutions in picture. The primary reason why OEMs should board an ALM system is to optimize their assets throughout their entire lifecycle without the need for manual processes. With recent advancements in technology, asset management systems have proven to add to the ALM best practices by providing accurate information on the asset condition, maintenance, repair history, licensing, and performance analytics—promising asset accuracy and efficiency. And this is all possible because of data.
The role of data behind AI ML-powered predictive/preventive maintenance, asset health monitoring, and location and condition monitoring is unavoidable. It is the base of a definitive ALM system. A smart IoT solution can not only monitor the performance of your assets but also deliver insights on how to improve them, which directly improves asset uptime.
Maximizing Your Asset Value
With tighter budgets for new asset acquisitions, OEMs’ customers are compelled to maximize the value of their existing asset inventories and extend asset lifecycles wherever possible. A robust, feature-rich Application Enablement Platform (AEP) like Flex83 empowers you to create and manage tailored Asset Lifecycle Management (ALM) solutions for your customers. By guiding decisions at every phase of the asset lifecycle, Flex83 empowers equipment manufacturers and enterprises to extract greater value, efficiency, and longevity from their assets and processes.