Industrial OEMs who have shifted towards smart manufacturing have already attained distinction from others who are in the queue. Now is the time when OEM executives should stand for adopting smart solutions and transforming their businesses, while gaining a competitive edge. Many have already improved the value chain performance over the last two decades, boosting the overall industry productivity by 47%. While traditional manufacturing is now taking a back seat, smart solutions with technological capabilities like AI and ML are helping the leading manufacturers to move to automation, precision quality control, and improved supply chains. However, developing these smart solutions is not a smooth process; it comes with its own set of challenges
In this blog, we will discuss why OEM leaders should aim for smart solutions, the benefits of these solutions, and the possible challenges that are keeping them from choosing these solutions.
Why OEM Leaders Need Smart Solutions
OEM leaders must embrace smart industrial solutions to stay competitive and drive innovation in today’s rapidly evolving industrial landscape. Now, when businesses are more focused on their customers’ needs, these solutions are paving the path for development. Traditional manufacturing solutions are often insufficient when it comes to efficiency, scalability, customization, and building newer revenue streams for industrial OEMs. On the other hand, smart solutions leverage real-time data, Machine learning, and Predictive analysis that help manufacturers anticipate and be responsive to customer needs, streamline their manufacturing needs, and minimize downtime. With smart manufacturing, businesses can create a completely integrated and automated manufacturing environment with collaborated and connected equipment, systems, and processes.
Almost 95% of manufacturers are already spending on smart manufacturing solutions; it is time for industry leaders to tap into their advantages without reflecting on possible consequences (which are minimal). These solutions will drive the future of manufacturing across the industrial landscape, avidly exploring the impenetrable advantages of technology.
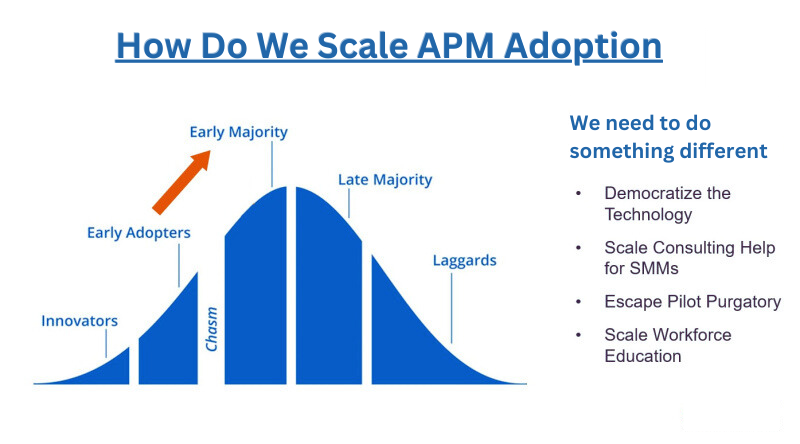
Benefits of Smart Solutions
Smart industrial solutions are pioneering the transformation of conventional manufacturing into smart manufacturing with fewer errors, streamlined operations, revenue generation, and increased customer-centric solutions.
1. Increased Efficiency and Productivity
Smart industrial solutions can automate redundant tasks, streamline workflows, and optimize resource allocation. For instance, a manufacturing factory that uses a smart inventory management system can constantly track its quantity in a large warehouse and automatically reorder materials when stock levels drop below a threshold, diminishing the time spent on manual inventory reviews and ensuring that warranty management is never halted or impacted.
2. Reduced Downtime and Improved Maintenance
Smart solutions powered by AI ML predictive maintenance capabilities can significantly reduce unexpected equipment failures. According to Accenture, predictive maintenance can reduce equipment failures by up to 70%, while AI-driven scheduling can increase asset utilization by 20-30%. OEMs can collect and analyze the data in real time to respond to critical issues immediately. They can further monitor equipment health with real-time data on performance and predict potential failures before they occur. This allows for timely maintenance, preventing unexpected shutdowns.
3. Enhanced Quality Control
AI ML-based smart industrial solutions can process, identify, and analyze data patterns that can be used to detect anomalies in equipment functioning and predict failures. For instance, an electronic manufacturer can identify any equipment breakdown in their product line in advance with predictive maintenance. It proactively schedules appointments with technicians and sends assistance with the right and required equipment to repair it on time, saving effort, time, and money to be used in manual checking.
4. Improved Supply Chain Management
Smart industrial solutions can enhance the visibility of all (logistics) product-related processes and coordination with constant tracking and logging. The data analytics provide real-time insights from the supplier to the customer, as well as inventory levels, shipment statuses, and supply chain bottlenecks. The route and state of transported goods are monitored to ensure their proper condition and delivery time.
5. Greater Flexibility and Scalability
Smart industrial solutions enable organizations to scale their operations more easily and adapt to changing demands. Cloud-based platforms and modular technologies can be adjusted to accommodate growth or shifting market conditions.
Challenges in Building Smart Solutions
The current technological complexities have forced industry leaders to face these tech disruptions and confirm they are staying ahead of their competitors. Most of them know adopting smart industrial solutions is the only possible way to gain this advantage. However, building smart solutions is not a one-day job; rather, it is a continued process, and this process comes with challenges.
1. Advanced Technical Skill Gaps
Business leaders often underestimate the change management and skills training needed to effectively implement and sustain new technologies like AI, Big data, and Machine Learning. To address this, OEMs can employ new talent with relevant industry credentials, upskill the existing workforce to become digitally literate and proficient in modern tools, or contract specialized experts to fill the resource gaps. By investing in these areas, organizations can better manage the transition and ensure they leverage new technologies effectively for long-term success.
2. Choosing the Wrong Technology Partner
A mismatch in goals or capabilities can lead to project delays, higher costs, and suboptimal results. If you choose to build an in-house IoT platform, it will cost you a fortune, greater time-to-market as well as a higher risk of failure. However, you can reduce cost and time-to-market with a low-code IoT platform but with a risk of feature limitations and inability to scale, which will eventually affect your business transformation journey. In comparison, you will achieve success with a Pro-Code Application Enablement Platform (AEP) that offers a complete customization opportunity with pre-built microservices, SDKs, and more. It costs you less and brings faster time-to-market compared to traditional methods.
3. Increased CapEx
Developing smart industrial solutions requires a significant initial investment in onboarding technologies, setting up a suitable infrastructure, and hiring skilled resources. This could compromise ROI. Some leaders might find this a blurry vision. Without a strategic investment plan, costs can become unmanageable, and competitive advantages may be limited.
4. Implementation Complexity
Smart manufacturing can enhance productivity, speed, and collaboration through automation, but scaling these benefits has been hindered by the complexity and cost of implementation, often involving intricate integrations by specialized system integrators and leading to vendor lock-in. This has resulted in slow adoption and disconnected systems reliant on manual data collection. Managing these complex integration changes can be challenging and time-consuming. For instance, an organization with legacy IT systems attempts to integrate a new AI-driven analytics platform. The integration process is more complex than anticipated, causing delays and requiring additional resources.
5. Legacy Processes and Systems
Existing legacy systems and infrastructures can hinder the adoption of evolving technologies, particularly when dealing with machines that have outdated or no digital interfaces. These systems often result in integration bottlenecks, interoperability issues, and data silos, hindering the overall information/data flow. While new IIoT sensors and edge gateway devices can help bridge the gap, updating technology remains complex due to numerous interdependencies. Another challenge with legacy systems is the hefty technical debt. These systems and processes require constant support, continuous maintenance, and security checks, which could add up to further costs.
6. Lack of a Link Between Technology and Business StrategyAround 50% of Industry leaders have spoken about not having a concrete strategy for developing smart industrial solutions for their manufacturing business. Without a clear connection between technology investments and business objectives, smart solutions can fail to deliver the expected benefits. Digital transformation requires a unified effort across all departments, with a strategy developed collaboratively by industry leaders and stakeholders in engineering, automation, IT, and other relevant areas. This ensures that technology investments are strategically focused on achieving a competitive edge and driving overall business success. For example, if a company invests heavily in advanced analytics tools without clearly defining how they align with its strategic goals, it will have zero or limited impact on overall business performance.
7. Cybersecurity and Data Privacy Concerns
Smart manufacturing is all about providing broader, secure connectivity among multiple equipment, processes, and systems, leveraging cloud services and the internet to cross-share data, which is further used for data-driven decisions. This process is forever prone to cyberattacks. Therefore, manufacturers need to implement cybersecurity measures that can prevent any possible attack on the data. Cybersecurity measures should protect intellectual property and data integrity, helping OEMs maintain business continuity and ensuring seamless functioning of the overall network.
Smart Industrial Solutions and the Future of Manufacturing
In conclusion, the roll-out of smart products and processes is not just a step but a leap toward achieving meaningful business transformation in the era of the Industrial IoT. For OEMs, embracing this shift is crucial for staying relevant and competitive in a landscape of rapid technological advancements and elevated customer expectations.
Onboarding an AEP (Application Enablement Platform) emerges as a particularly well-suited approach, offering a robust framework that aligns with the need for customization, scalability, and revenue generation, transforming the overall business process. Pro-code platform providers, in particular, stand out by delivering significant value through their comprehensive investment in technology, adaptability to diverse needs, and enhanced ownership of the development process. Their solutions facilitate the rapid deployment of sophisticated, scalable, smart solutions while ensuring OEMs maintain control over their innovations. As OEMs navigate the complexities of smart industrial solutions development, leveraging these advanced platforms will be instrumental in driving successful IIoT-driven business transformation and securing a competitive edge in the marketplace.